Top 10 razloga zašto vam je još uvek potreban PLC
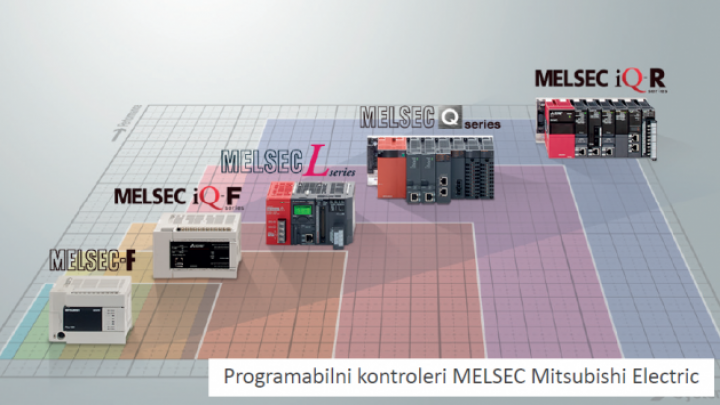
Postojalo je vreme, ne tako davno, kada je PLC važio kao jedina primenjiva opcija za kontrolu u industrijskoj automatizaciji. Danas inženjeri imaju više izbora u obliku industrijskih PC računara, “soft” PLC-a i panel PC računara koji oponašaju funkcionalnost PLC/HMI kombinacije. Inženjeri, koji su tome skloni, mogu izgraditi vlastite kontrolere na bazi Raspberry Pi pločice.
Uprkos pojavi ovih novih mogućnosti, još uvek postoje mnogi opravdani razlozi za korišćenje PLC-a. Ovde je deset najvažnijih:
1. Bezbrižnost
PLC i PC računari su prošli dug razvojni put od svojih skromnih početaka, ali postoji velika razlika u tome kako će se ta rešenja dalje razvijati, a to ima značajne implikacije za dugoročnu podršku. Kontrolisana evolucija PLC-a znači da proizvođači mogu pružati i pružaju podršku za svoje proizvode tokom dugog vremenskog perioda, u pogledu hardvera i softvera.
To u slučaju Mitsubishi-a znači, da možemo, na primer, aplikacijski program, iz 20-godišnjeg FX PLC-a prebaciti u potpuno novi FX5U. Aplikacija na novom kontroleru može početi s radom skoro trenutno. Tako nešto je nezamislivo pomoću rešenja baziranog na industrijskom PC-u.
Postoje mnoge grane industrije gde taj nivo podrške ne samo da je poželjan nego spada u osnovne zaheve. U industriji voda, vode se razgovori da bi dobavljači trebalo da osiguraju podršku za upravljačke sisteme u trajanju do 20 godina. Naravno, upravljački hardver će se menjati tokom tog vremena, ali PLC korisnici mogu biti mirni znajući da će softver uvek biti prenosiv na najnoviji kontroler.
2. Urođena robusnost i pouzdanost
Savremeni industrijski PC osigurava stabilnu računarasku platformu i bilo bi nepravedno sugersati da će se „smrzavati i rušiti“ poput kućnog PC-a. Međutim, industrijski PC nije ni izbliza ravnopravan s PLC-om. Operativni sistem (na industrijskom PC-u) za rad u realnom vremenu izvršava se uz Windows OS i projektovan je da osigura isti nivo robusnosti kao kod procesorske jedinice PLC-a.
Kada bi PC radio u potpunoj izolaciji, možda bismo mogli zaključiti raspravu o pouzdanosti. Međutim, takav kontroler ne postoji; tu su periferije za spajanje, ulazi/izlazi prema mreži i ostale komponente za komunikaciju, od kojih svaki zahteva “drivere” učitane u računar. Hoće li “driveri” za sve te proizvode biti kompatibilni i temeljno testirani? Čini se malo verovatno. Problemi mogu nastati pri svakom ažuriranju “drivera”.
Povremeni padovi sistema na industrijskom računaru su neizbežni. Šta bi to moglo značiti za upravljanje procesom? S druge strane, kada ste zadnji put čuli da je bilo potrebno resetovati PLC nakon pada sistema - verovatno nikada...
3. Proširivanja i prilagodljivost
Brojčano najprodavaniji PLC, koji obuhvataju najširi spektar aplikacija, su oni s 40 ili manje U/I tačaka. U takvim aplikacijama, PLC predstavlja vrlo povoljno rešenje, mnogo povoljnije nego ekvivalentni sistem na bazi PC-a. Međutim, ta ista osnovna platforma je proširiva na nekoliko desetina hiljada U/I tačaka, a korisnik ima mogućnost prebacivanja programa na veći PLC, koristeći isto programsko okruženje i prednosti potpuno modularnog hardvera.
Potencijal za prilagođavanja PLC je ogroman, a načina za proširenje funkcionalnosti je bezbroj, sve to bez potrebe za napuštanje zajedničke platforme.
4. Programiranje
Čak i danas, na svakog inženjera koji završi fakultet i dobro vlada strukturiranim programskim jezicima i svakog inženjera vičnog C ili C ++, verovatno postoji preko deset onih koji žele koristiti samo “ladder” logiku, posebno za aplikacije s manjim brojem U/I tačaka.
Pored toga, postoje aplikacije koje su na početku jednostavne, možda pisane u “ladderu”, ali vremenom rastu i razvijaju se koristeći proširivanja PLC platforme, mogućnost pisanja upravljačkih programa u obliku strukturiranog teksta i jednostavno korišćenje funkcijskih blokova, što će uštedeti mnogo truda pri programiranju.
Mitsubishi nudi mogućnost programiranja PLC-a u C ++, i na taj način objedinjuje fleksibilnu hardversku platformu i programski jezik visokog nivoa. Naravno, te iste mogućnosti programiranja su dostupne na PC platformi, ali je nivo modularnosti, proširivanja i prilagodljivosti koje nude programski alati za PLC znatno veći.
5. Integracija s drugom opremom za automatizaciju
Mnogi inženjeri automatike, nemaju potrebe raditi izvan portfolija jednog dobavljača ukoliko dobavljač, kao npr. Mitsubishi, ima mogućnost odgovoriti na svaki zahtev vezan uz HMI, frekventne regulatore, servo pogone, “motion” kontolere, “safety” aplikacije, robote, niskonaponsku opremu za distribuciju i upravljanje potrošnjom električne energije i CNC sisteme. Kako su sve ove komponente dizajnirane da rade zajedno, inženjeri koriste sve prednosti "uključi i radi” integracije.
Postoje dobavljači industrijskih PC računara, koji mogu tvrditi da nude sličan spektar proizvoda, ali ih sigurno nema mnogo. Ali, pravi izazov dolazi kada treba integrisati komponente različitih proizvođača.
Kod modernog PLC-a, integracija hardvera drugih proizvođača je jednostavan zadatak. Može li se isto reći za integraciju na PC platformu? Hoće li “driveri” za module drugih proizvođača sigurno raditi? Koliko će biti potrebno uložiti truda za konfiguraciju? I možda još važnije, hoće li biti osigurana trajna kompatibilnost kroz ceo radni vek upravljačke platforme?
6. Mogućnosti
Što se tiče snage i performansi, Mooreov zakon o razvoju računara se jednako odnosi na PLC kao na PC. Zaista mnogi ljudi zaboravljaju da je moderan PLC snažan računar. Najnoviji model Mitsubishi FX PLC-a je, na primer, 150 puta brži od prvobitnog.
Koliko je moćan moderni PLC postaje jasno kada pogledate brzinu izvršavanja instrukcija, koja kod najnovijih izvedbi nudi vreme izvršavanja kraće od nano sekunde. Možda je PC moguće naterati na sličnu efikasnost, ali PLC je ima čim je pušten u rad.
Zatim, tu je povećana brzina sabirnica i sposobnost brze sinhronizacije višestrukih U/I tačaka, čime se postiže bolji odziv upravljačkog sistema. Nešto slično puno je teže postići izvan PLC okruženja.
7. Sigurnost
Dolaskom moćnih virusa kao što su Stuxnet, svi su shvatili da su i sistemi za automatizaciju postali mete, kao i da hakeri žele ugroziti poslovanje velikih preduzeća ili vitalne komunalne usluge. Zbog poznatog operativnog sistema i ranjive mreže, računar može predstavljati “stražnji ulaz” upravljačkog sistema za onoga ko pokušava provaliti.
Nasuprot tome, operativni sistem PLC, znatno su manje vidljivi za spoljašni svet i to je tradicionalni sloj zaštite od zloupotreba. To ne znači, da proizvođači PLC-a uzimaju sigurnost zdravo za gotovo. Mitsubishi, na primer, omogućuje zaštitu programa lozinkom i različite nivoe pristupa za korisnike.
Zatim, daljinski pristup se može regulisati tako da se pravo na pristup dodeljuje samo za određene IP adrese. Na taj način se štiti PLC softver i ostatak upravljačkog sistema čak i kod jako umreženih aplikacija.
8. Intelektualno vlasništvo
Ako razmotrimo pojam sigurnosti u širem smislu, dolazimo do problema intelektualnog vlasništva. Za preduzeća koja deluju na svetskom nivou, s globalnim razvojnim timovima ili isporučuju sisteme u inostranstvu, problem predstavlja kopiranje softvera od strane trećih osoba, koje im omogućuje da vrlo brzo razviju jeftiniji konkurentski proizvod.
Kod svih upravljačkih platformi to je valjan razlog za zabrinutost, dok su proizvođači PLC napravili značajne korake za rešavanje tog problema. U proizvodima Mitsubishi, u hardver i softver se ugrađuje šifrirani kod, koji se može izvršiti u određenom trenutku. To može značiti da je sistem otvoren za programere i integratore sve do kraja puštanja u pogon, a nakon toga se uključuje zaštita sistema od dalje interakcije.
9. Održavanje
Svaki sistem automatizacije, bez obzira na platformu, zahteva rutinsko održavanje; npr. kontrolu hardvera ili nadogradnju softvera, postupno proširenje u skladu s potrebama aplikacije ili pak zamenu neispravnih komponenti. Lakoća kojom se to može postići je glavna odlika PLC-a. Programi i postavke za sve komponente mogu biti sačuvani na SD karticu preko utora na procesorskom modulu.
Čak i u slučaju ispada procesorskog modula PLC-a, moguća je brza zamena, a izvorni program se učitava sa sigurnosne kopije na SD kartici. Ponovno pokretanje aplikacije je vrlo brzo.
U isto vreme, nema potrebe za stalnim ažuriranjima firmware-a koji muče sisteme bazirane na PC-u i sa sobom nose stalnu brigu da će se sistem srušiti zbog nekompatibilnosti. Sama činjenica da je računar višenamenski sistem, jedan je od njegovih najvećih nedostataka u automatizaciji procesa.
10. Smanjeni IT zahtevi
Jedno od pitanja u bilo kojem sistemu automatizacije, pogotovo kada dolazi do integracije nivoa proizvodne automatizacije i viših nivoa, jeste raspodela odgovornosti između inženjera zaduženih za automatizaciju i IT tima. Tu može dolaziti do tenzija, ali još važniji problem je gotovo neizbežno međusobno nerazumevanje.
Kod automatizacije bazirane na PLC-u, granice između automatike i IT-a su čiste uz malu ili nikakvu potrebu za angažmanom IT tima na nivou automatizacije proizvodnje. Nadalje, pomoću rešenja poput Mitsubishi MES modula koji se priključuju na matičnu ploču PLC-a i pružaju izravnu vezu s bazama podataka na višim nivoima, celi slojevi PC računara mogu u potpunosti biti eliminisani iz sistema, što granicu između upravljačkog i informatičkog sistema čini jasnijom.
Vidimo, dakle, da postoji mnogo razloga zbog kojih će PLC ostati temelj upravljačkih sistema, čak i ako ne uzmemo u obzir pitanja poput redundancije, sigurnosti itd. Valja napomenuti i sposobnost modernog PLC-a da obavlja mnoge složene matematičke funkcije koje su u prošlosti mogle biti izvršavane jedino na sistemu baziranom na PC-računaru.
Naravno, izbor odgovarajućeg rešenja treba napraviti prema zahtevima svakog pojedinog sistema automatizacije, no PLC nudi mnogo razloga da bude izabran kao platforma.
INEA SR d.o.o.///Karađorđeva 12/217///Smederevo///Republika Srbija
Tel: +381 26 4615 401